How Defoamers Are Used to Prevent Foam in Food and Beverage Production
How Defoamers Are Used to Prevent Foam in Food and Beverage Production
Blog Article
Discover the Leading Benefits of Making Use Of Defoamers in Industrial Processes
The utilization of defoamers in industrial procedures offers an array of compelling benefits that can improve operational effectiveness and item quality. By efficiently managing foam manufacturing, these representatives not just maximize product circulation but also contribute to considerable expense decreases and enhanced sustainability. The effects of taking on defoamers might be more profound than initially perceived.
Enhanced Process Efficiency
Optimizing industrial processes commonly entails dealing with lathering problems, which can impede operational effectiveness. Foam formation can conflict with the appropriate performance of devices, lower the reliable utilization of resources, and complicate the monitoring of vital specifications. By executing defoamers, industries can efficiently reduce these problems, resulting in structured procedures and enhanced efficiency.
Defoamers work by destabilizing the foam framework, enabling fast collapse and considerable reduction in foam volume. This activity not only enhances the circulation of products with equipment, such as activators, pipes, and mixers, but additionally reduces interruptions brought on by foam overflow. Subsequently, devices downtime is reduced, enabling a much more effective and continuous manufacturing process.
In addition, the use of defoamers can bring about minimized energy intake. With less foam to handle, pumps and compressors can run much more successfully, leading to lower functional prices and a general renovation in process throughput. Inevitably, the tactical usage of defoamers not only addresses immediate foaming difficulties yet likewise adds to an extra reliable industrial environment, promoting an affordable benefit in a demanding market.
Improved Product High Quality
The combination of defoamers in commercial processes plays an essential role in enhancing product top quality. By properly managing foam formation, defoamers add to the uniformity and uniformity of end products. Too much foam can cause aeration, which adversely impacts the structure and stability of formulas, specifically in industries such as food and drugs, coverings, and beverages.
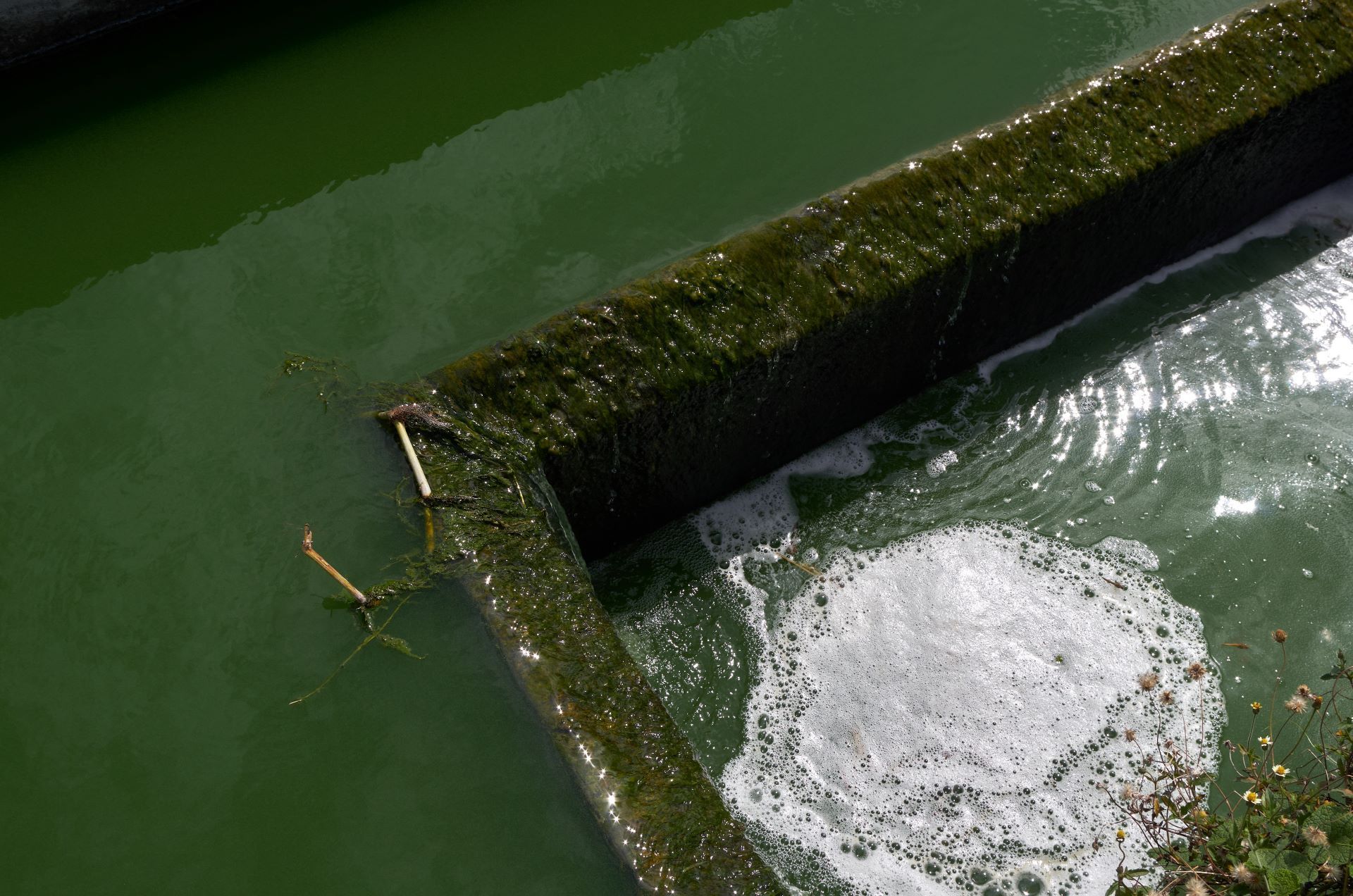
Furthermore, defoamers promote better blending and dispersion of ingredients, leading to homogeneity in formulas. This is essential in applications where exact active ingredient ratios are critical for efficiency and safety and security. Furthermore, the elimination of foam can lower the threat of contamination during production, further securing item integrity.
Ultimately, by enhancing item quality, defoamers not just enhance consumer satisfaction but also strengthen brand track record. Their function in keeping high-grade standards highlights their relevance in contemporary commercial processes.
Expense Decrease Benefits
Carrying out defoamers in commercial processes can bring about considerable cost decrease advantages. By properly managing foam formation, defoamers minimize product loss during manufacturing, therefore enhancing material usage. This reduction in waste converts straight into reduced basic material prices, improving total operational efficiency.
Furthermore, using defoamers can lower energy consumption. Extreme foam can impede devices efficiency, bring about raised energy requirements to keep production levels. By reducing foam, defoamers help with smoother procedures, enabling Web Site machinery to run much more effectively and decreasing energy expenditures.
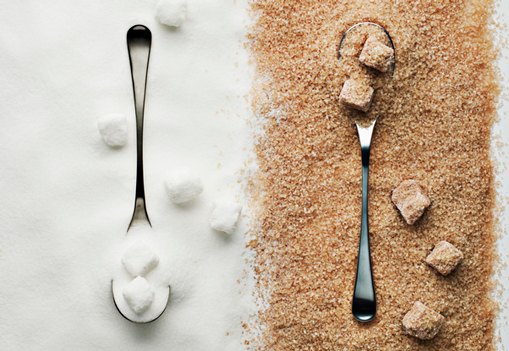
In addition, defoamers can shorten handling times. Foam can develop added challenges that extend manufacturing cycles. By making use of defoamers, markets can enhance their procedures, causing faster turn-around times and improved throughput. This efficiency not only speeds up manufacturing however likewise enables companies to meet market needs more quickly.
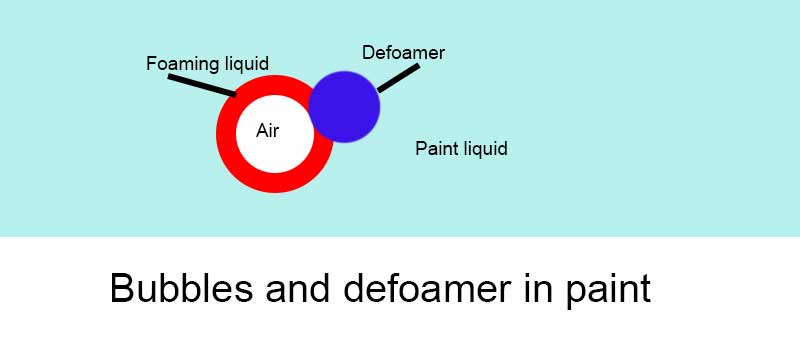
Environmental Influence Mitigation
In industrial processes, the usage of defoamers plays an important function in mitigating environmental influences linked with foam generation. Foam can lead to substantial operational ineffectiveness, resulting in increased emissions and waste generation. By successfully managing foam, defoamers help keep procedure effectiveness, therefore lowering the total environmental impact of procedures.
Additionally, excessive foam can overflow containment systems, leading to spills that might contaminate dirt and water sources. Defoamers assist decrease this danger by making certain that frothing does not go beyond prescribed limits, advertising conformity with ecological guidelines. This positive approach not just safeguards ecosystems yet likewise improves the sustainability of industrial methods.
In addition, making use of defoamers can lower energy consumption in numerous processes. defoamers. Reducing foam formation reduces the need for additional energy-intensive procedures, such Get More Info as boosted agitation or pumping, which might or else be essential to handle foam. Consequently, the adoption of defoamers straightens with more comprehensive sustainability objectives by promoting energy performance while lessening the carbon impact of industrial activities.
Ultimately, incorporating defoamers right into commercial operations is a strategic procedure that sustains ecological stewardship and accountable source administration.
Flexibility Across Industries
Across different sectors, defoamers demonstrate remarkable adaptability, adapting to the certain needs of varied applications. In the food and beverage market, for instance, defoamers are crucial to keeping product high quality by preventing foam formation throughout processing, which can impact texture and flavor. In a similar way, in the pharmaceutical industry, defoamers make certain the stability read of formulas, boosting product effectiveness and uniformity.
In the chemical production realm, defoamers help with smoother procedures by minimizing foam in reaction vessels, therefore boosting yield and decreasing downtime. The paper and pulp market relies upon defoamers to enhance the effectiveness of pulp handling and paper manufacturing, guaranteeing ideal item honesty. Additionally, in wastewater treatment facilities, defoamers play a crucial duty in regulating foam during aeration processes, resulting in enhanced therapy end results.
The versatility of defoamers reaches the oil and gas sector, where they aid in managing foam in drilling fluids and production processes. By tailoring formulas to satisfy certain market demands, defoamers function as crucial tools that enhance operational effectiveness, item top quality, and overall procedure performance throughout a multitude of industries. Their versatility highlights their worth in modern-day commercial applications.
Verdict
In final thought, the use of defoamers in industrial processes presents various advantages, including improved efficiency, improved item top quality, substantial expense reductions, and positive environmental influences. Their capacity to successfully manage foam formation adds to operational continuity and source optimization. Additionally, the versatility of defoamers throughout varied industries underscores their critical duty in promoting sustainable techniques and success. The integration of defoamers stands for a strategic technique to addressing obstacles related to foam monitoring in various making environments.
Inevitably, the tactical use of defoamers not just addresses prompt frothing obstacles but also contributes to a much more effective commercial ecological community, fostering a competitive advantage in a demanding market.
In industrial processes, the use of defoamers plays an important function in mitigating ecological effects connected with foam generation. By properly regulating foam, defoamers aid keep procedure performance, consequently lowering the total ecological impact of operations.
Furthermore, in wastewater treatment facilities, defoamers play a vital duty in regulating foam throughout oygenation processes, leading to improved treatment end results.
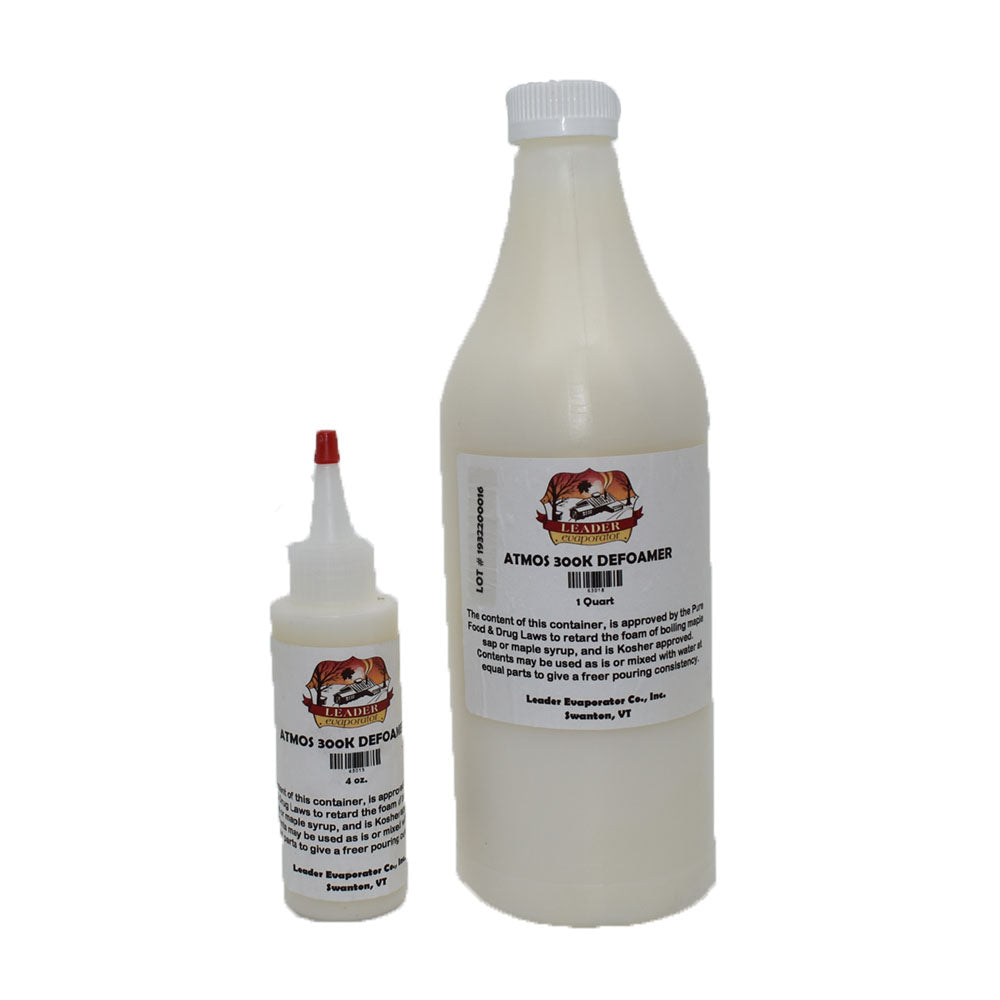
Report this page